Cushion, pt.2
- Jerry Schultz, P.E.
- Aug 25, 2016
- 5 min read
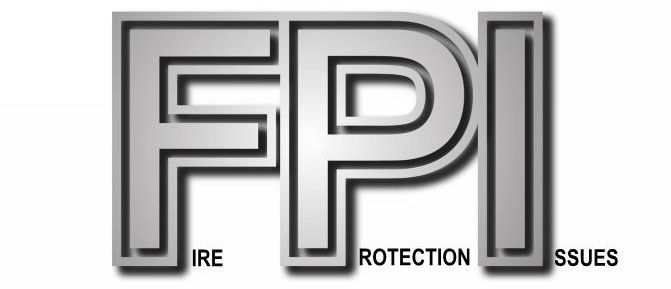
In my last blog post, I wrote about a cushion on water supplies and raised the question if the system is properly designed, is a cushion (hydraulic buffer) required? I pointed out that NFPA 13 appears to be heading down a path where we will soon be mandating a cushion. In an earlier post, I addressed NFPA 25 and identified a gap in the standard. This blog post will attempt to address both of these issues together and make a point that even with a cushion, the need for diligence in reviewing NFPA 25 results, along with an understanding of basic water supply is critical. Let us also agree that NFPA 25 is NOT a design, construction, or installation Code or Standard. Designers are not required to meet NFPA 25 during design, inspectors are not required to verify installations during the punch list phase of a project, and final acceptance tests are not required by NFPA 25. NFPA 25 assumes that the original installation was installed and approved correctly, and that the existing system is considered adequate/acceptable. NFPA 25 is an Inspection, Testing, and Maintenance (ITM) standard and cannot apply to systems that have not yet been built. It is probably the ultimate retroactive standard because the latest edition is what the system is to be analyzed against.
Not too long ago, one of my clients who operates a building in a large Midwestern city, assigned an individual to the property. This individual was required to read the sprinkler gauge on a quarterly basis and noticed that the gauge that had read 65 psi for the last 5 years was suddenly reading 35 psi. He quickly contacted us and asked if there was a problem with the system. (As an aside, once I was brought in to review a hospital’s ITM program and found that the inspector, in doing their monthly inspection had recorded 0 psi on the gauge for the last 9 months. He was doing what he was told, recording pressures.) Back to the original story. We got involved with the project and identified that the water supply had been decreased by 30 psi by the city. It seems that this one area of the large city had its own supply and the city had decided to connect this leg back to the remainder of the underground grid which was at the lower pressure. This lower pressure obviously impacted the sprinkler system (again, last month we talked about 5 psi or 10% cushion, never a 30 psi cushion) and caused the sprinkler system to be deficient (demand exceeded supply).
Upon further investigation, I received from the local municipality’s water department, a document written in the 1920’s indicating a legal covenant between the municipality and the original building owner that the water department was only required legally to provide 20 psi at the facility. Regardless of the fact that the sprinkler system which was installed in 1992, had been provided a minimum pressure of 65 psi and had used this value in their design of the sprinkler systems.. The municipality in essence, exceeded their legally mandated covenant and now by reducing the pressure, it was up to my client to adjust and redesign the system. In this case, we had to design a fire pump for the existing system. Needless to say, we designed the pump using the covenant number (20 psi).
In another Midwestern village, the municipality elected to decrease the water supply by 15 psi in order to reduce leaks on their piping. This was done due to a concern about the age of the pipe. Once again suddenly the sprinkler systems are under-designed.
In another situation, my client is connected to a 100 year old underground pipe that appears, based on a hydraulic gradient analysis to have an equivalent C factor of 60. This 300 foot long pipe runs for a portion under the highway and is scheduled for replacement, but the project has been delayed for 5 years while funding keeps getting cut. The friction drop through this pipe is impacting the sprinkler system so that once again, a system is under-designed. On this one, static pressure is where it should be. It is only when flowing water that one sees the deficiency.
Municipalities across this country are facing an aging infrastructure and a need for the water departments to reduce costs, this seems to be a re-occurring theme, affecting the fire protection of structures and I wonder, the fire service capabilities of the communities that they serve.
War stories exist everywhere and I am sure that you have some yourself. I walk into the building and check the main drain tags and notice that the system used to have a static pressure of 90 psi and for the last several years, static pressure is 65 psi. Yet the hydraulic placard (yes it is present and legible) reads:
This system is designed to provide a density of 0.20 gpm per square foot over the most remote 1500 square feet when supplied with water at a rate of 595 gpm at 78 psi…
It should be obvious to all that if the system requires 78 psi at 595 gpm and I only have 65 psi at 0 gpm, there is a problem. Yet the main drain test had changed in 2002 so for 13 years, the sprinkler system water supply was no longer adequate and nobody commented.
California drought conditions, hydrants flowing water over the hot summer leading to excessive seasonal low conditions, water departments decreasing water supplies to reduce leakage and save money, the aging infrastructure and pipes deteriorating are all conditions that the cushion we have discussed both in this and last month’s blog cannot address. So we go back to, who should notice this? Whose responsibility is it to identify a problem with the existing water supply?
Getting back to my point, NFPA 25, Standard for the Inspection, Testing and Maintenance of Water Based Suppression Systems, does not require the contractor performing the inspection, testing, and maintenance of these systems to evaluate the system’s water supply, (let alone if the hazard of the facility has increased), thereby making the system less than adequate. In a previous blog, I addressed the hole in NFPA 25 where no one assesses the adequacy of the system but here is a gap that is easier to address. This is the purpose of NFPA 25, it is used to evaluate “wear and tear” on the system components as described in an NFPA Journal column two years ago. Someone who is qualified needs to review the inspection report and identify these issues. A person recording weekly pressures of 0 psi is obviously qualified to record pressures but not qualified to read and understand the data collected. The decrease in a water supply for whatever reason is becoming a bigger and bigger issue. Owners need to understand what information is being collected and review those results so that there is always an adequate water supply for fire protection and fire service. The cushion discussed in last month’s blog does not account for the deteriorations we are seeing.
It mostly works well when someone who understands the importance of the information gathered is involved, someone who can interpret the data collected, reviews the gathered data, and can add context around what that data is saying. The individual recording the weekly pressure notices the decrease like my client did. The individual who reviews the main drain test notices that the pressure has decreased below what it has been for years. The only way to address this is to ensure that a qualified individual is reviewing reports and not just filing these in a drawer. The information is there but it needs to be pulled together.
I find it interesting that as I write these blog posts, they are so interrelated. These last two, which started to address a deterioration of the water supply, highlights the need for someone knowledgeable to review the data gathered in an NFPA 25 inspection.
As always, I welcome your comments: j.schultz@the-fpi.com