NFPA 25 and Sprinkler System Adequacy
- Jerry Schultz, P.E.
- Apr 20, 2016
- 6 min read
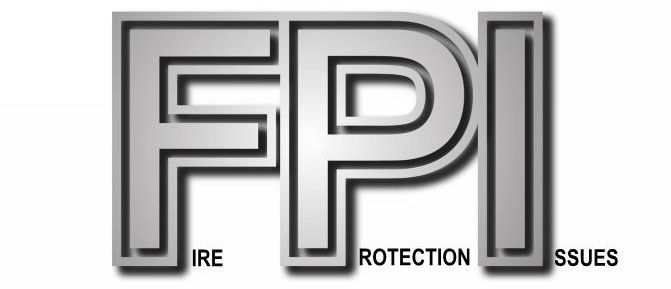
Today, let’s talk about NFPA 25, Standard for the Inspection, Testing and Maintenance of Water Based Fire Protection Systems and discuss one of the biggest gaps in the industry. I believe that most people in the fire protection industry, understand and accept this gap but does that make it right and how can the fire protection industry deal with such a large gap in ensuring proper protection? Several years ago, there was a round-table discussion organized by NFPA that took place in Chicago where the gap was a key point in the discussion. It was decided at that point, 25 was not going to address the issue and the issue would have to be addressed in another manner.
The gap which I speak of is, who inspects the sprinkler system for adequacy? Who reviews the building to assess changes? Who evaluates the protection in the building and comes up with the conclusion that the system is adequate and that the building is properly protected? It clearly states in the Appendix A.1.1.3.1 of NFPA 25 that it is the property owner or designated representative’s responsibility to evaluate the adequacy of the design. There is some merit to this argument. For example, an AHJ in Illinois can require, per the Professional Engineering Act, a technical submission by a registered engineer developing the fire suppression system’s criteria for a facility. The layout of the fire suppression system has to be done by either a licensed engineer or a NICET Level 3 individual. During the initial design, there are attempts to ensure that the system being provided is adequate for the hazard.
It is after the initial design that the gap starts to appear. In a typical commercial office building, where reconfiguring of offices is routine, one would not anticipate the fire hazard to significantly change. The firm doing the inspection may notice sprinklers missing from rooms due to wall reconfiguration or similarly sprinklers too far from walls. In a warehouse however, the occupancy can have significant changes occurring. Storage creeps higher, racks are introduced in lieu of general storage, racks are reconfigured so that aisles are narrower and perhaps the biggest one, the commodity itself changes. This can be as simple as the “plasticization” of society. Everybody knows that plastics will burn “hotter” or more severely than ordinary combustibles. “Everybody” knows this, but is the warehouse manager aware of the implications? I cannot forget telling an owner that their sprinkler system was under-designed for the hazard when their domestic garden hose reels went from all metal to all plastic. I had to deal with three comments, all from the same client—
What are you talking about? I am still selling hose reels.
I want that previous inspector because he never cited me.
How can you say I am under-designed? I have not had a fire here in 20 years!
As I stated in the beginning, NFPA 25 clearly indicates that adequacy is not part of the inspection process. Starting in Chapter 1:
1.1.3.1 This standard does not require the inspector to verify the adequacy of the design of the system.
The burden is placed on the owner (or designated representative) to watch what is being stored and how it is being stored in Chapter 4.
4.1.6 Changes in Occupancy, Use, Process, or Materials. The property owner or designated representative shall not make changes in the occupancy, the use or process or the materials used or stored in the building without evaluation of the fire protection systems for their capability to protect the new occupancy, use, or material.
To further amplify that 25 never meant to have the assessment of the adequacy be part of the Inspection, Testing and Maintenance it states in Section 4.1.6.1 that the evaluation above is not part of the normal inspection required by NFPA 25 but does go on to say what it should address including occupancy changes or process changes.
And then NFPA 25 goes one step further (Section 4.1.7.1) and tells what the owner should do to address changes in the hazard including promptly taking steps to evaluate the adequacy and if the evaluation reveals the system is inadequate, the owner shall make the required corrections.
If the issue is still not clear, the committee makes it extremely evident with Annex comments:
A.1.1.3.1 The requirement to evaluate the adequacy of the design of the installed system is not a part of the periodic inspection, testing, and maintenance requirements of this standard. However, such evaluation is the responsibility of the property owner or designated representative as indicated in 4.1.6 and 4.1.7. A.4.1.6 The inspections and tests specified in this standard do not address the adequacy of design criteria or the capability of the fire protection system to protect the building or its contents. It is assumed that the original system design and installation were appropriate for the occupancy and use of the building and were approved by all applicable authorities having jurisdiction. If no changes to the water supply or to the building or its use have transpired since it was originally occupied, no evaluation is required. If changes are contemplated, it is the owner’s responsibility to arrange for the evaluation of the fire protection system(s). Where the inspections and tests specified in the standard have been contracted to a qualified inspection provider or contractor, it is not the role of the inspector or contractor to determine if any changes have been made or the subsequent evaluation of the fire protection system. The evaluation of any building changes should be conducted before any proposed change is incorporated and should utilize the appropriate installation standard and input from applicable authorities having jurisdiction. Fire protection systems should not be removed from service when the building is not in use; however, where a system that has been out of service for a prolonged period (such as in the case of idle or vacant properties) is returned to service, it is recommended that a responsible and experienced contractor be retained to perform all inspections and tests.
The gap should be obvious. The owner is paying for the Inspection, Test and Maintenance of his sprinkler system. He is hiring a licensed qualified contractor and is not being told that his sprinkler system is under-designed. We expect him to recognize the change in the hazard and take steps to evaluate it. This from an individual who may have been convinced by Hollywood that when the sprinkler system actuates, all sprinklers will begin to flow. (It must be understood that this comment does not apply to clients of The FPI.)
If not the owner and not the contractor, then who (or whom)? The insurance company? They are setting insurance rates on buildings based on the adequacy of the system. If a system is inadequate, they may just adjust the rates. In addition, certain insurance companies do not have a qualified fire inspection program. The building inspector? In most municipalities they don’t have the time to do follow up inspections. The consulting engineer? They have to be retained to do this (speaking as a consulting engineer it would probably make sense to make it a mandatory law that consulting engineers should inspect each building annually and write a report on the adequacy, but alas, not many people agree with me.)
Without the requirement that a consulting engineer be involved, how can a municipality be comfortable that the system is still adequate for the hazard? One way that seems to be gaining momentum is through a high-piled storage permit process. Certain municipalities require an annual application for a high-piled storage permit. Table 1.12.8(a) in the 2015 edition of the NFPA Fire Code (NFPA 1) and Section 105.6.23 of the International Fire Code requires an operational permit to “use a building or portion thereof as a high piled storage area exceeding 500 square feet”. It is this permit, if done properly, that can be used to evaluate the existing sprinkler system. This should not be a fundraiser for the municipality (submit your fee and we will file your drawings) but should be a way to evaluate what is present and if it is adequate. Certain municipalities require a drawing to be submitted identifying the storage arrangement, commodity classification and protection provided such that a knowledgeable individual can review the information and reach a decision if a problem warranting further investigation is necessary.
There are several key steps in using a high-piled permit in this way. These steps include:
The high-piled permit request form must clearly state what information is required. This information must include:
Commodity classification
Storage arrangement (racks-single, double-row, multi-row, shelf storage, pallets, etc.)
Aisle widths
Encapsulation
Solid shelving
Storage height
Sprinkler criteria
In general sufficient information to review and assess the adequacy.
A qualified individual working for the city must review the criteria and assess the design.
Random follow up inspections should be done to ensure that the information provided is correct.
The owner spends money buying a properly designed sprinkler system for their building. It is necessary that some form of evaluation be done to ensure that as conditions change, the system is still capable of controlling the fire. John R. Hall reports in the document U.S. Experience with Sprinklers, two reasons for sprinkler system failure are: Not enough water discharged to control the fire; and inappropriate system for type of fire. Both of these reasons can be reduced by the review of the adequacy of the system.
As always, I welcome your comments: j.schultz@the-fpi.com